連續(xù)沖壓模具的基本知識與應用技巧
作者:佚名|分類:百科常識|瀏覽:86|發(fā)布時間:2025-03-12
隨著五金制造行業(yè)工人工資水平的持續(xù)上漲,降低沖壓生產(chǎn)的人力成本已成為制造商亟待解決的問題。在眾多解決方案中,采用連續(xù)模是較為常見的方法之一,因為它能夠有效構建低成本且高效率的自動化生產(chǎn)線。然而,由于連續(xù)模需要高度精確和復雜的部件設計,在實際應用過程中存在諸多挑戰(zhàn)。
首先,當沖壓模具包含較多小孔時,小型凸模不宜過長。這種情況下,可以通過將不同尺寸的凸模制成階梯式來解決,以避免所有凸模同時承受最大壓力,并減少對設備的要求。值得注意的是,較小的凸模需要制造得更短一些,而較大的則可以做得稍長些,兩者之間的高度差應等于板材厚度。
其次,在連續(xù)模具中增加擋料、側刃等步距定位裝置是必要的。通過這些裝置確保條料能夠準確地進入下一道工序,這對于保證產(chǎn)品質量至關重要。常用的定位方法包括固定式擋料器和移動式的側邊調整器。
再者,為了防止材料在沖壓過程中因切屑飛濺而受損或影響模具的穩(wěn)定性,在設計時應加入防跳屑結構。這可以通過改進刀口形狀、添加吹氣孔等方式實現(xiàn),確保廢料不會干擾到工件表面的質量和成品率。
另外,連續(xù)模中的載體設計也是一個關鍵環(huán)節(jié)。由于各工序間的零件傳輸依賴于帶材上的搭邊余料(即載體),因此其穩(wěn)定性直接關系到整個生產(chǎn)過程的精度和效率。為了保證足夠的強度和剛性,通常會采用加大搭邊尺寸或使用雙面載體等方式。
此外,在連續(xù)模具的設計中,快速拆裝功能及零件防呆設計同樣重要。這有助于在維修過程中迅速更換損壞部件,并避免因操作失誤導致的額外損失。
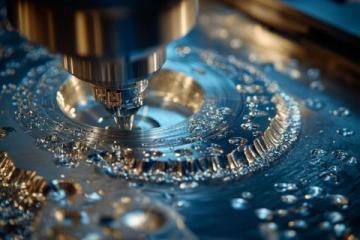
以上就是關于提高五金制造領域沖壓效率的一些方法和建議。如果您對此話題感興趣或有相關疑問,歡迎隨時留言交流!
(責任編輯:佚名)